智能控制乳化罐,提升生产效率与质量
点击次数:3295 更新时间:2024-08-14
在21世纪的制造业浪潮中,智能化转型已成为不可逆转的趋势。随着工业4.0概念的深入人心,各行各业纷纷探索如何运用先进的技术手段提升生产效率、优化产品质量、降低成本,以实现可持续发展。在化妆品、食品、医药、涂料等众多领域,乳化过程作为核心工艺之一,其效率和质量控制直接影响到最终产品的品质和市场竞争力。因此,智能控制乳化罐作为智能制造领域的新兴力量,正逐步成为行业升级的重要推手。
一、乳化技术概览
1.1乳化工艺简介
乳化是指两种或多种不相溶的液体(通常是油相和水相)通过搅拌、剪切或超声等方式形成稳定乳状液的过程。在工业生产中,乳化罐作为核心设备,承担着将原料混合、分散、乳化的任务,是生产高质量产品的关键环节。传统乳化罐大多依赖于人工控制和机械搅拌,存在能耗高、混合不均匀、生产周期长等问题。
1.2发展历程
随着材料科学、控制技术及自动化水平的提升,乳化罐也经历了从简单到复杂、从机械控制到智能控制的转变。早期主要依赖于电机驱动搅拌器进行混合,效率低且难以实现精准控制。后来,随着变频技术、PLC(可编程逻辑控制器)等技术的应用,开始具备初步的自动化控制能力。而今,智能控制乳化罐融合了物联网、大数据、人工智能等先进技术,实现了全过程的智能化、精细化操作。
二、核心技术
2.1传感器技术的应用
内部集成了多种高精度传感器,如温度传感器、压力传感器、流量传感器及液位传感器等,能够实时监测罐内物料的状态变化。这些传感器将采集到的数据实时传输至控制系统,为智能决策提供依据。例如,温度传感器可监控物料加热或冷却过程中的温度变化,确保乳化反应在最佳温度条件下进行;流量传感器则能精确控制各种原料的投加量,确保配比精确无误。
2.2智能化控制系统
乳化罐的控制系统基于先进的PLC或工业PC,集成了自动化控制算法和专家系统。该系统能够根据预设的工艺参数和实时监测到的数据,自动调整搅拌速度、加热功率、进料速率等关键参数,以实现理想的乳化效果。同时,控制系统还具备故障诊断与预警功能,能够在第一时间发现并处理潜在问题,确保生产安全稳定进行。
2.3大数据与人工智能技术
乳化罐不仅仅局限于简单的自动化控制,它还借助大数据和人工智能技术,对生产过程中的海量数据进行深度挖掘和分析。通过对历史数据的比对和分析,系统能够识别出不同工况下的控制策略,并通过自学习不断优化控制逻辑。此外,利用人工智能的预测算法,系统还能提前预测并应对可能的生产异常情况,进一步提升生产效率和产品质量。
三、应用优势
3.1提升生产效率
通过精确控制各项工艺参数,显著缩短了乳化过程的时间。同时,由于系统具备自动化和智能化特性,能够实现24小时不间断生产,极大地提高了设备利用率和生产效率。此外,系统还具备远程控制功能,用户可通过互联网随时监控生产状态并调整参数,进一步提升了生产灵活性。
3.2优化产品质量
乳化罐能够确保原料配比的精确性和工艺参数的稳定性,从而减少了因人为操作失误或环境变化导致的产品质量波动。通过实时监测和调控罐内物料状态,系统还能有效防止乳液分层、团聚等不良现象的发生,提高了产品的稳定性和均匀性。此外,智能化的控制策略还能针对不同产品需求进行定制化生产,满足市场的多元化需求。
3.3降低生产成本
在提升生产效率和产品质量的同时,也显著降低了生产成本。一方面,通过优化控制策略和节能降耗技术的应用,系统能够有效降低能耗和物料消耗;另一方面,智能化的维护和保养功能能够延长设备使用寿命并减少故障停机时间,从而降低了维护成本和生产损失。
3.4提高安全性与环保性
乳化罐配备了全面的安全保护和环保监控系统。在安全性方面,系统具备故障预警和紧急停机功能,能够在第一时间发现并处理潜在的安全隐患;在环保性方面,系统能够精确控制物料的投加量和废弃物的排放量,减少了对环境的污染和破坏。
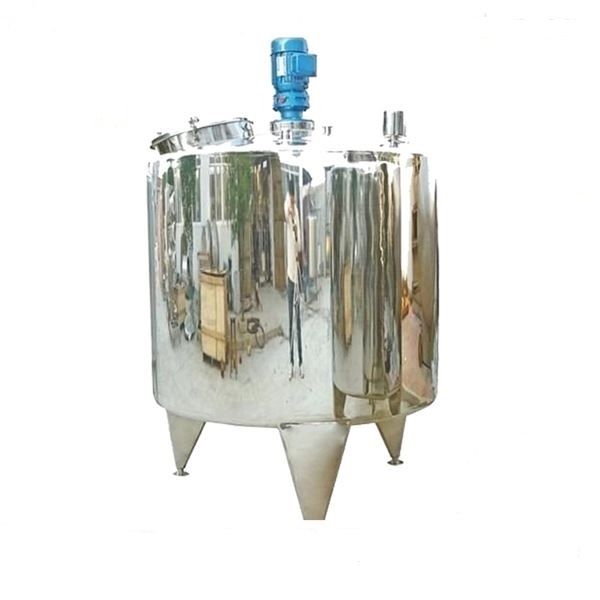